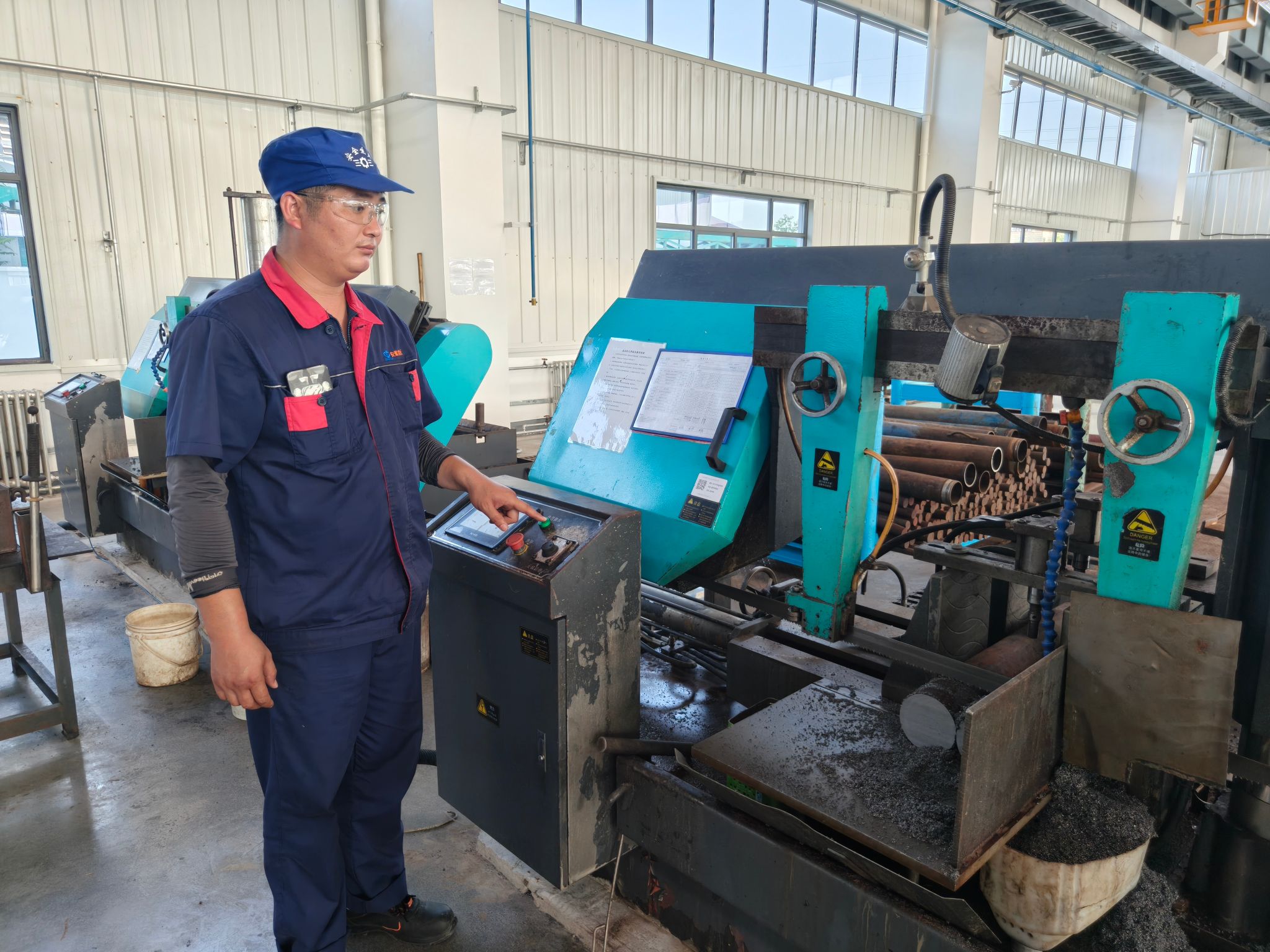
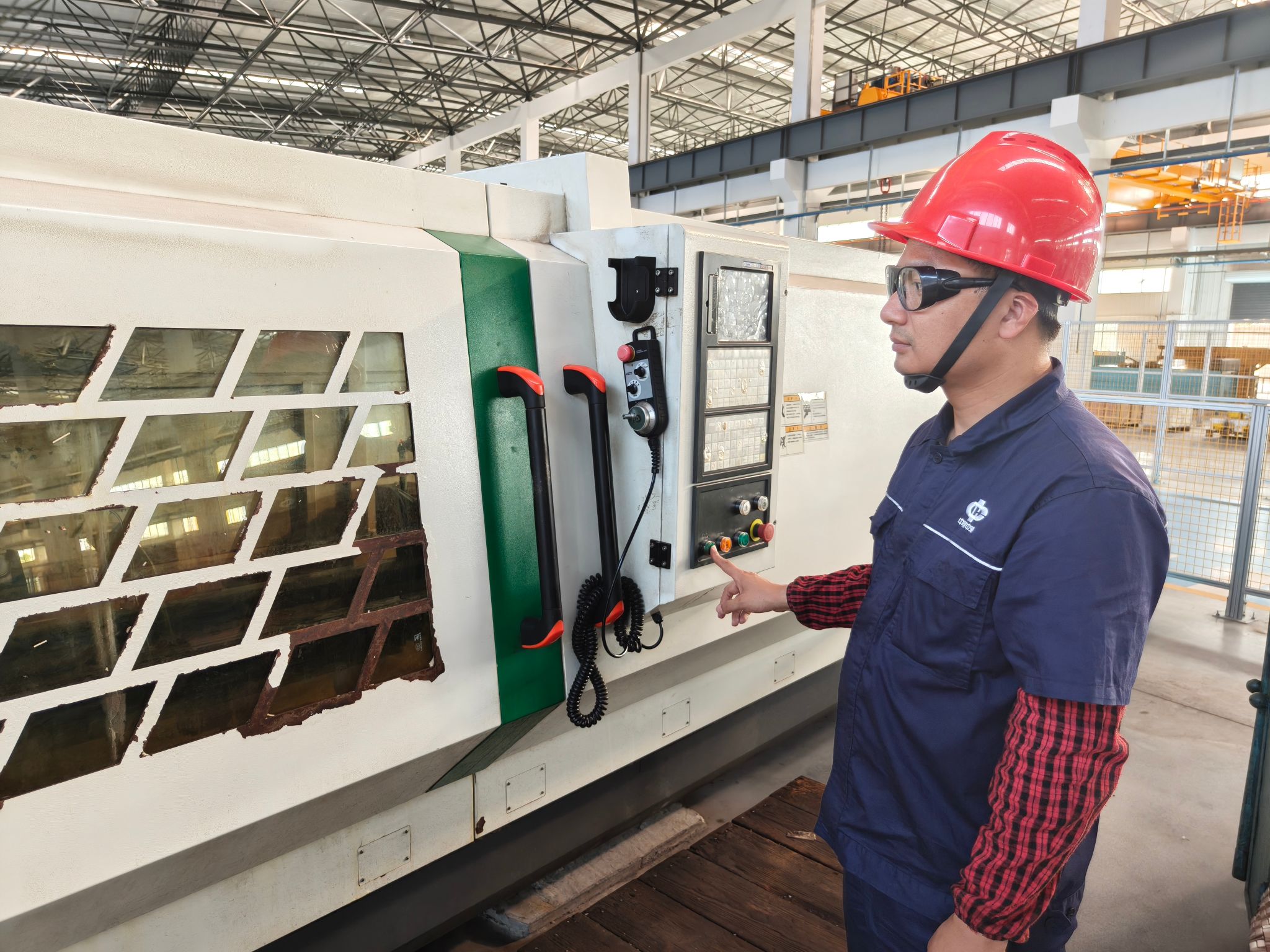
大批量配件的数控切削加工不仅是满足对矿服务的需求,更是打造设备检修精品工程的前提条件。6月份,设备维修公司综修车间积极组织好工种间的统筹协作,将单轨吊小车轮各零件的数控切削作为自制件高质量加工的示范样本,严格执行“源头把关、基准统一、编程简练、尺寸精准、轮廓顺畅”的工艺要求,组织相关技术人员和机加工生产骨干一起下功夫、上措施、求实效,为设备检修的高质量发展注入新活力、新效能。
以数控机床循环绿键的“一键到底”为追求目标,综修车间机加工生产骨干们自觉将一丝不苟、精益求精的工作态度融入到锯、钻、车各工序,将自制精品加工件的责任意识融入到每一步按键操作之中。
一是坚持毛坯料形位公差的源头把关。在第一道下料工序时,对大直径毛坯圆钢的弯曲部位进行调整校平,同时调节好带锯条的张紧程度,确保数控锯床绿键按下后的每一件小车轮毛坯料的两侧面都能够保持平行度和平面度公差要求。
二是坚持毛坯料钻、车工序的基准统一原则。在数控加工中心利用U钻打孔的时候和在数控车床进行内孔车削的时候,所采用尺寸规格完全一致的垫块工装,有效控制住了加工中心绿键按下后U钻打孔的同轴度和深度。
三是充分发挥出G71代码编程时,简洁强大的特殊型面加工功能。通过切削用量的合理分配和G42代码的刀尖补偿作用,在保证尺寸精度的前提下,使单轨吊小车轮外廓锥度和圆弧型面实现了顺畅衔接,以技术含量提升每个自制件的产品质量。